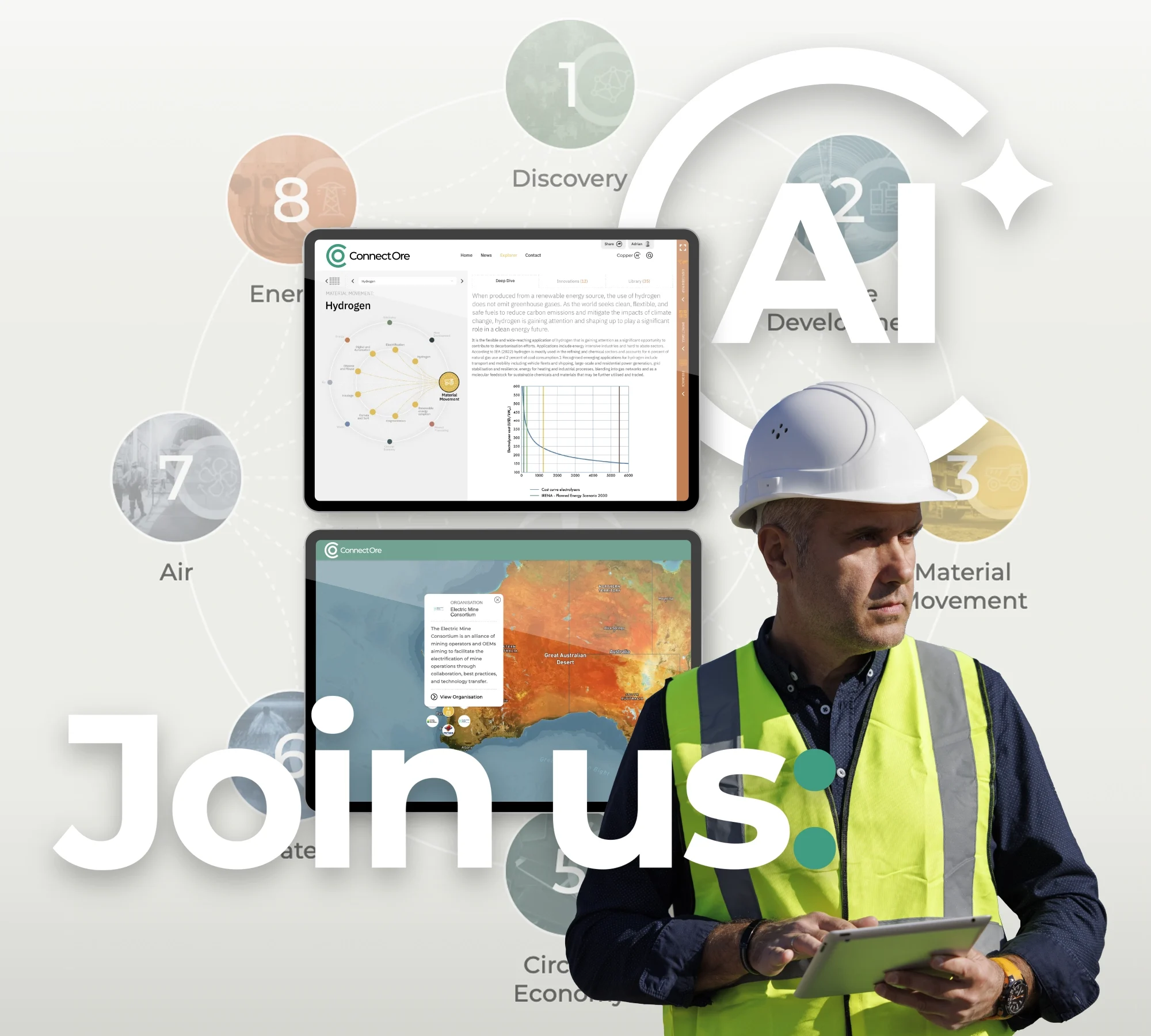
Issue 02 - June 2025
The mining industry is experiencing a paradigm shift in how it approaches tailings management, driven by ESG priorities, resource optimisation and the urgent need for critical and strategic minerals in the global energy transition.
The industry faces a dual imperative: mitigating environmental risk from legacy and existing waste streams and unlocking economic value through valorisation or repurposing of tailings. Due to metal being produced at different grades through the lifecycle of a mine and the economics of mining, the ore within a tailings storage facility (TSF) may vary by physical properties, mineralogical composition, volume, and method of storage and disposal. The environments in which TSF are located also vary, requiring individual approaches to each site1.
ICMM and a consortium of industry and research partners developed the Global Industry Standard on Tailings Management (GISTM). The standards cover the entire TSF lifecycle from site selection to post-closure2.
The establishment of the Global Tailings Management Institute (GTMI) in January 2025 is demonstrating collaboration across the industry and is accelerating accountability, mandating third-party audits for tailings facilities globally3. Significant innovations are emerging across technological, regulatory, and commercial domains to mitigate, reprocess, and repurpose waste streams, reflecting a broader industry shift, and demand for the adoption of circular economy (CE) principles. The market for tailings management solutions, valued at $15 billion in 2025, is projected to grow at 7% annually, reaching $25 billion by 20334.
This Pulse briefing examines the state of tailings mitigation and valorisation, highlighting key stakeholder priorities, existing and emerging technologies, and evolving industry opportunities and challenges. With critical and strategic mineral demand surging for clean energy technologies, the opportunity for tailings valorisation can bridge resource optimisation, security and sustainability, and transform liabilities into assets.
Top of Pulse, regarding tailings valorisation for mining executives
Mining Executives are prioritising strategies that align with ESG criteria while enhancing profitability through sustainable practices. Technologies that reduce waste, valorise or convert tailings into valuable by-products such as construction materials or alternative metal recovery are of interest to industry.
Transitioning to circular economy (CE) models is increasingly important for governments, industry, and society to reduce waste and environmental impacts and optimise resource use. The mining sector, traditionally a major waste generator, has a significant role to play by managing waste from extraction processes and reusing raw materials.
Mining waste includes sub-economic materials produced during exploration, extraction, and processing, such as gangue, overburden, and tailings. These materials may contain chemical additives and pose environmental and operational challenges due to their composition, volume, and method of storage. A TSF can have large footprints, storing both solid waste and contaminated water, which has long term risks of polluting environmental and community ecosystems.
Tailings management is a complex issue, especially in arid regions where water is scarce. However, tailings also represent a potential resource. Technologies for tailings reprocessing - either by reintegrating material into existing circuits or adapting facilities at mine closure - are increasingly presenting practical solutions, with emerging innovations on the rise.
As copper ore grades decline, waste volumes will grow unless the industry adopts technological solutions for waste minimisation and repurposing. While there have been advancements in primary ore processing to drive operational efficiency and resource recovery, and the recent development of global standards, a coordinated industry-wide shift toward waste management and re-use is still emerging. Collaboration across industry, regulators, and researchers is essential to transform tailings from liabilities into assets. Recognising this, industry bodies like the ICMM and initiatives such as Amira Global, Canada’s Green Mining program, BHP’s Tailings Challenge, India’s Critical Mining Mission 5 6, and BHP’s Think and Act Differently initiative are examples of collaborative innovation development.
GTMI, established in January 2025 is an independent, multi-stakeholder organisation based in South Africa, co-founded by the International Council on Mining and Metals (ICMM), the United Nations Environment Programme (UNEP), and the UN-backed Principles for Responsible Investment (PRI). Its mission is to enhance the safety of mine tailings facilities worldwide by overseeing the implementation and assurance of the Global Industry Standard on Tailings Management (GISTM), aiming for zero harm to people and the environment through independent audits and certifications2.
The GTMI’s certification requirements have elevated governance standards, compelling executives to reassess long-term liability costs3. Regulatory and policy shifts to address critical mineral demand are also driving the application of new technologies and processes to tailings facilities for the extraction of critical minerals like cobalt and lithium.
Executives are also exploring the management of existing facilities and mitigating storage risks through the application of filtration and dry stacking methods to be operational at scale7. Partnerships with OEM solution providers like Metso and FLSmidth are critical to deploy modular solutions, while legacy site remediation - especially for sulphidic tailings - remains a pressing challenge due to acid mine drainage risks8 9.
Incorporating novel technologies for tailings valorisation faces barriers like high capital costs, operational risks, regulatory compliance, and site-specific challenges. The industry must tactically pilot and demonstrate innovations to overcome these hurdles, emphasising government and cross-industry collaboration to enable a supportive innovation ecosystem.
Innovations - Horizon 1
(Available in-market now and in the next 5 years)
A strategic focus on sulphidic tailings addresses a critical industry need, as these materials often contribute to acid mine drainage and long-term environmental liabilities. Technologies that offer both environmental remediation benefits and potential economic returns through metal recovery, are creating a value proposition for multiple stakeholder groups10.
Market ready solutions include modular dewatering and re-processing technologies (flotation). Filtered tailings systems, such as FLSmidth’s EcoTails®, are reducing storage footprints by 50% through dry stacking methods 11. Auxilium Technology Group’s modular systems convert 90%+ of tailings into carbon-negative construction materials, with active deployments in the Americas12 13.
Select solutions include:
- FLSmidth: EcoTails® and GeoWaste™ systems for dry stacking, reducing storage footprints by 50%4.
- Metso: Reprocessing technologies extracting copper and gold from legacy tailings, cutting costs by 30% compared to virgin ore processing8.
- EnviroGold Global: NVRO Process™ for sulphidic tailings remediation and metal recovery, addresses the dual challenge of environmental remediation and resource recovery, targeting gold, silver, copper, zinc, and rare earth elements from legacy mine sites and is advancing toward commercial deployment9.
- Stantec & Auxilium: Modular systems converting 90%+ of tailings into carbon-negative construction materials13.
- Clariant: Tailings treatment technologies in Brazil, focusing on flotation and dewatering14.
Phibion (Accelerated Mechanical Consolidation): Phibion’s AMC technology accelerates tailings consolidation, improving water recovery and facility stability15.
Innovations - Horizon 2
(Evolving over the next 5 - 10 years)
The technological landscape for tailings valorisation in horizon 2 encompasses several innovative approaches addressing different aspects of waste conversion.
Advanced technologies under development include algae-based systems for environmental remediation, electro-osmosis dewatering for improved consolidation, and accelerated mineral carbonation for carbon sequestration applications21.
Current and emerging solutions include Tersa Earth’s microbial fuel cells for metal recovery and water neutralisation, piloted with BHP12. CoTec Holdings’ fine-tailings processing for iron ore pellets is advancing toward permitting in Quebec12. Jord International's NovaCell Technology targets a more pragmatic approach by addressing modular grinding and flotation systems for improved metal recovery from tailings[16].
Select solutions include:
- CO2Valorize: Mineral carbonation integrating tailings with CO₂ to produce low-carbon cement, entering industrial trials17.
- University of Queensland: Research on critical mineral recovery from Australia’s Altas of Mine Waste, supported by government partnerships18.
- Weir Group: Coarse particle flotation (CPF) enhancing metal recovery while enabling hydraulic dewatered stacking4.
- NEMO Consortium: Bioleaching technologies for cobalt and zinc extraction from sulphidic waste, funded by EU Horizon 20209.
- Luleå University: TAILOR-MADE project testing enzyme-assisted carbon capture in Swedish tailings19 [20].
- Jord International's NovaCell Technology: Targets energy reduction in grinding for improved metal recovery from tailings. Pilot tests have shown promising results in reducing operational costs, with market readiness expected within two to three years16.
- Tersa Earth’s microbial fuel cells use naturally occurring microbes to recover valuable metals and neutralise acidic water in tailings, generating electricity as a by-product. Piloted with BHP, the technology offers a sustainable, low-energy solution for mine waste remediation and is expected to reach market readiness in 3–5 years22.
- Greensnow (Bio Intelligence Leaching Solvent): Greensnow’s BILS technology employs bio-based solvents to extract rare earth elements (REEs) from tailings, achieving 25% higher recovery than conventional methods23.
Horizon 2 Snapshot - Geoscience Australia, Atlas of Australian Mining Waste
One of the challenges of reprocessing tailings is the highly varied profile of a TSF. As ore is processed at different percentages depending on current economic and market settings, the composition of remaining metals in the tailings will vary.
Geoscience Australia has partnered with researchers at the School of Engineering at RMIT University and the Sustainable Minerals Institute at The University of Queensland to combine world-class mineral resource advice and mineral systems understanding with world-leading mine waste research to generate Australia’s first national Atlas of Australian Mine Waste (Atlas). The Atlas identifies potential new opportunities for minerals supply from secondary sources. It helps support the sustainable and economic recovery of critical and strategic minerals extraction from, and appropriate management of, mine waste. The Atlas is an interactive online mapping tool that provides governments, industry and the community with accurate information about Australian mine tailings, waste rock, smelter residues and related mine waste materials24.
The Atlas describes different waste types, such as tailings, flotation tailings, and leach residues, as well as the storage type or structure and any rehabilitation undertaken across many different commodities, including copper.
Find out more: Geoscience Australia, Atlas of Australian Mining Waste
Innovations - Horizon 3
(Emerging over 10 years and beyond)
Long-term breakthroughs aim to eliminate tailings for the mining value chain entirely and secondary recovery technologies include modular systems, bioleaching, phytomining and electrodialysis.
The ICMM’s Precision Mining Initiative explores in situ recovery methods to bypass waste generation12. Luleå University’s enzyme-assisted carbon capture, using biocatalysts to accelerate CO₂ mineralization in tailings, could transform storage facilities into carbon sinks8. Molten oxide electrolysis, under research at the University of Canterbury, seeks to extract titanium from slag with near-zero waste4.
Industry and research consortia plays an important role to support Horizon 3 technology development. The Sustainable Technologies for Calcined Industrial Materials in Europe (STOICISM) Project, are bringing together novel technologies and demonstration sites across the resource supply chain. STOICISM research objectives included opportunities for waste minimisation and recycling, including waste characterisation, recovery technologies and demonstration plants, and lifecycle analysis focusing on carbon footprints across the supply chain. The results of this project were disseminated to the Industrial Minerals Association Europe (IMA Europe)25. Programs like BHP’s ‘Tailings Challenge’ also aim to bring innovative technologies to reprocessing tailings. This program saw the trial and testing of two innovative reprocessing technologies26.
In Europe A.SPIRE has been established to manage the Processes4Planet Partnership, representing process industries (including minerals) to enable the development of technologies and best practices along the value chain to ‘close the loop’ through collaborative research and development and investment in new technologies through its Hubs4Circularity27. The European Commission has issued the Extractive Waste Directive, which established standards for characterising mining wastes and includes directives for recovery and recycling. This has been supported by the Commission’s circular economy action plan (CEAP), which embeds extended producer responsibility in key sectors/products, including electronics and batteries, and increases responsible sourcing of materials such as copper for these products28.
Horizon 3 technologies remain conceptual but promise systemic shifts in mining practices.
Select solutions include:
- ICMM: Precision Mining Initiative targeting in situ recovery methods to eliminate tailings generation29.
- University of Canterbury: Molten oxide electrolysis research to extract titanium from slag with near-zero waste30.
- MRIWA: Electro-osmosis dewatering trials to accelerate consolidation using renewable energy31.
- University of Pennsylvania: Carbonation-based rare earth extraction from legacy tailings, requiring policy reforms for viability.
- Monash University (Algae-Based Remediation): Monash’s Tailings Group explores algae systems to bioleach metals and sequester carbon in tailings ponds. Early-stage trials show promise and work required for scalability32 33.
The Pulse for Policymakers and the Sector
Collaboration between governments, miners, and tech firms is critical to scale solutions while addressing community concerns over legacy sites.
Inconsistent global standards and conflicting international treaties have created barriers to an industry-wide approach to tailings reprocessing and reuse however this is shifting with GTMI of the oversight implementation and assurance of the Global Industry Standard on Tailings Management (GISTM)2.
Policymakers are enacting tailings-specific jurisdictional frameworks, such as India’s 2025 policy to recover critical minerals from secondary sources, and which also eliminates import duties on recycling materials6 34. Canada’s push for a national tailings inventory aims to identify reprocessing opportunities, particularly for Indigenous-led projects35 36. The EU’s Recovery and Resilience Facility funds initiatives like Sweden’s TAILOR-MADE, integrating bioengineered carbon capture into tailings management19 20. Regulatory sandboxes in Australia and Chile are testing novel technologies, though fragmented standards persist.
Conclusion
Tailings valorisation is redefining waste as a resource, balancing ESG compliance with economic opportunity.
Horizon 1 technologies offer immediate risk reduction, while Horizon 2–3 innovations promise transformative efficiency gains across tailings mitigation and value accretion. Success hinges on cross-sector partnerships, aligned policies, and sustained R&D investment. As the GTMI enforces global standards, the industry must prioritise transparency and lifecycle cost analysis to secure social license and accelerate the transition to zero-waste mining. The integration of circular economy principles and critical mineral recovery positions tailings valorisation as a cornerstone of sustainable resource management in the 21st century.
Sources
1 International Copper Association Australia, Roadmap to Zero: Material Movement
2 ICMM - Global Industry Standard on Tailings Management
3 New independent institute to drive and assess the implementation of ...
4 Tailings Management Solution 2025-2033 Overview
5 National Critical Mineral Mission - PIB
6 First-ever tailings policy to recover critical minerals in the works - Tradelink Publications
7 Dry Stacking of Filtered Tailings for Large-Scale Production Rates over 100,000 Metric Tons per Day: Envisioning the Sustainable Future of Mine Tailings Storage Facilities
8 How to generate value from tailings with reprocessing to be future ready? - Metso
9 Bioleaching of cobalt from sulfide mining tailings: a mini-pilot study
10 EnviroGold Global Advances NVRO Process for Strategic Resource ...
11 International Mining - Filtering through: Trends in tailings management
12 Innovation comes to tailings management - Mining Technology
13 Mining Magazine - Turning tailings waste into value
14 Mine Tailings Valorization - Term - Energy - Sustainability Directory
17 Valorization of CO2 for low carbon cement
18 Geoscience Australia, Atlas of Australian Mining Waste
19 Mining tailings are being upgraded – in order to capture carbon ...
20 TAILOR-MADE | Luleå tekniska universitet
21 Alternative Use of Tailings and Waste - Minerals Research Institute ...
25 Industrial minerals sector contribution to circular economy
26 BHP tailings challenge: Repurposing copper tailings
28 EUR-Lex - 52020DC0098 - EN - EUR-Lex (europa.eu)
29 Tailings Management: Good Practice Guide - ICMM
30 Producing technology-critical materials for a low-emission future
31 Accelerating Consolidation of Mine Tailings using Electro-osmosis Dewatering Technology
32 Innovation in Tailings Management | A Sustainable Mining Breakthrough
33 MONASH Tailings Goal - ICMM
34 Budget 2025: Policy soon to recoup critical minerals from byproducts
35 Waste Not | Action Canada - PDF
36 Unlocking Critical and Strategic Mineral Opportunities in Canada's ...